
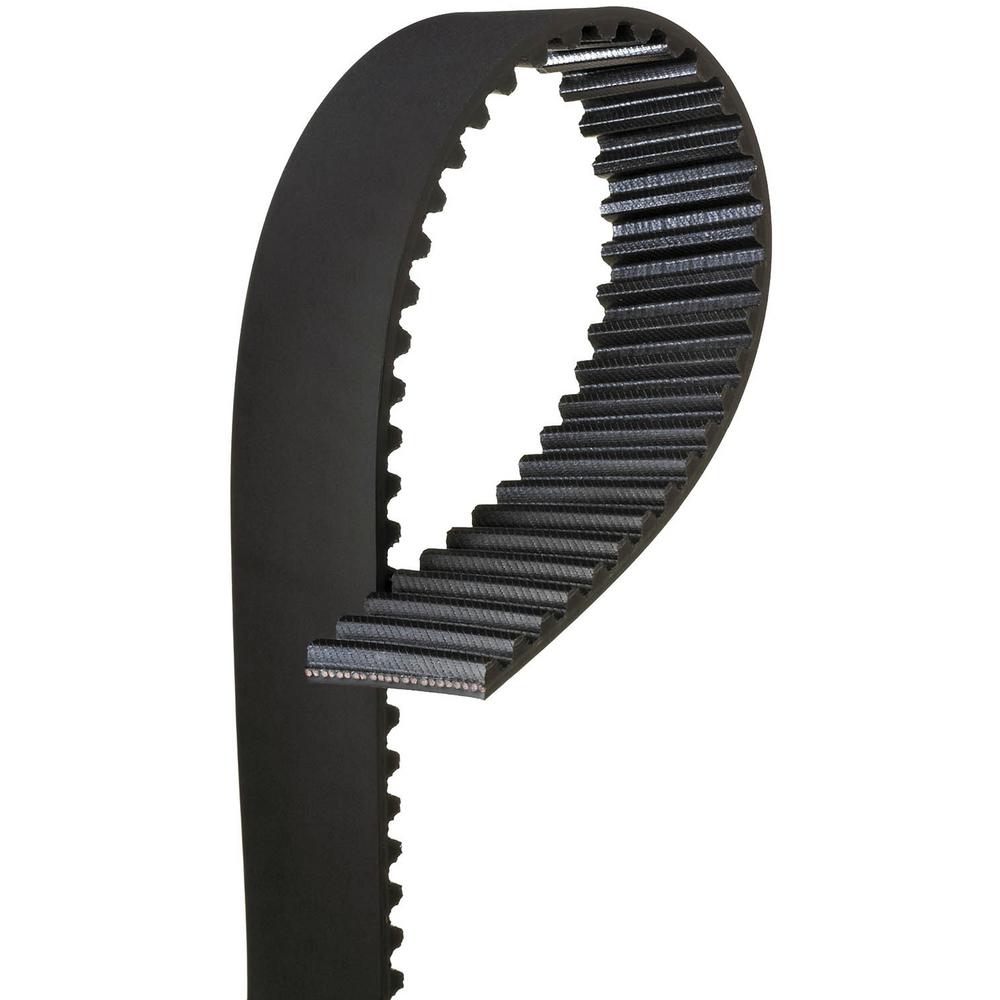
The joined configuration avoids the need to order multiple belts as matched sets.īanded V-belts should not be mounted on deep-groove sheaves, which are used to avoid turnover in standard V-belts. The intermittent forces can induce a whipping action in multiple-belt systems, sometimes causing belts to turn over. These belts are suited for severe duty applications, including shock and high starting loads.īanded V-belts solve problems conventional multiple V-belt drives have with pulsating loads.
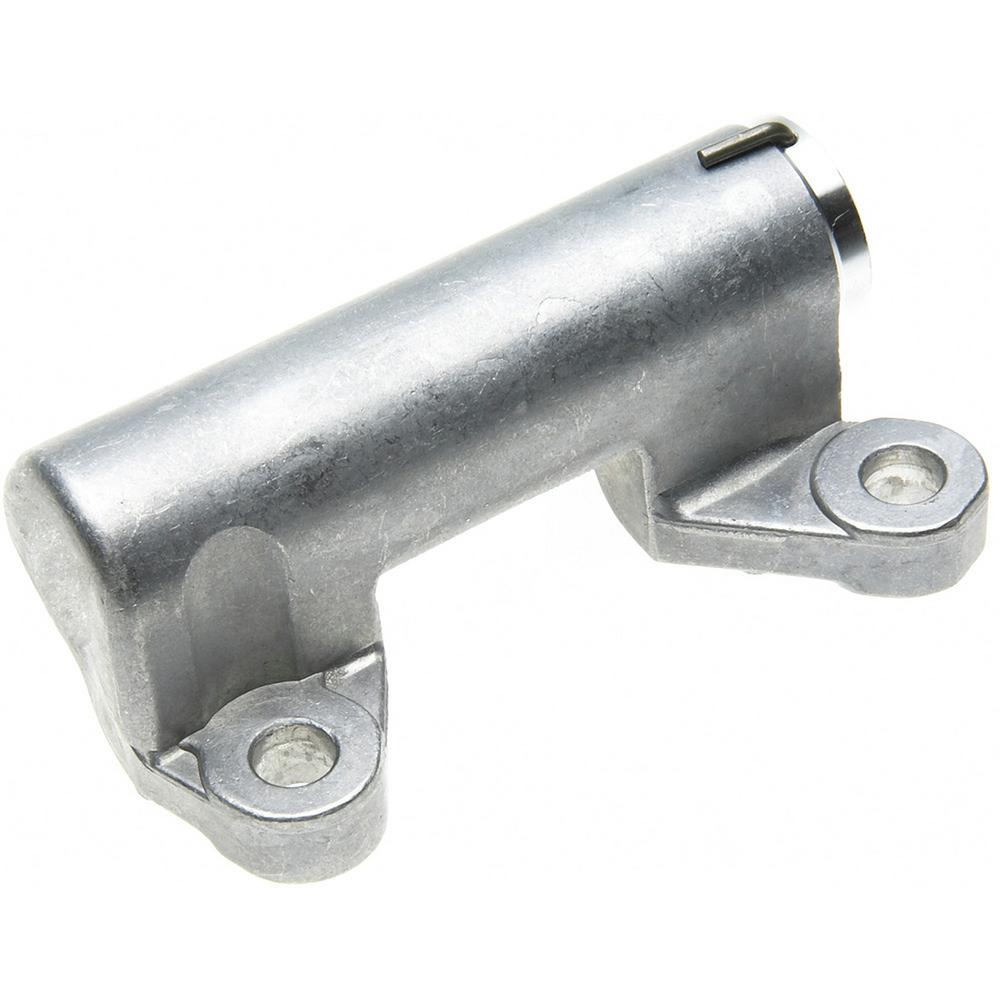
They have a greater depth-to-width ratio, placing more of the sheave under the reinforcing cord. Narrow V-belts, for a given width, offer higher power ratings than conventional V-belts. Multiple A or B belts are economical alternatives to using single-belt C, D, or E sections. The larger C, D, and E sizes generally are not used in single-belt drives because of cost penalties and inefficiencies. 3).Ĭlassical V-belts are frequently used individually, particularly in A and B sizes. This geometry multiplies the low tensioning force to increase friction force on the pulley sidewalls (Fig. The biggest operational advantage of a V-belt is the wedging action into the sheave groove. The V-shape makes it easier to keep fast-moving belts in sheave grooves than it is to keep a flat belt on a pulley. V-belts are commonly used in industrial applications because of their relative low cost, ease of installation, and wide range of sizes (Fig. At higher ratios, longer center distances or idlers placed on the slack side of the belt create more wrap around the smaller pulley to transmit the required load. Speed ratios usually should not exceed 6:1. Continuous, smooth-running applications are preferred. The grooves nearly eliminate the effects of dirt, dust, oil, and grease and help reduce the noise level.įlat belts operate most efficiently on drives with speeds above 3000 fpm. The air cushion reduces friction between the pulley and belt. In high-horsepower applications and outdoor installations, longitudinal grooves in the belt surface reduce the air cushion flat belts generate. Flat belts are forgiving of misalignment however, proper alignment improves belt life.ĭifferent flat belt surface patterns serve various transmission requirements. Belt tracking is improved by crowning at least one pulley, usually the larger one. Pulley alignment is important to flat belts. Good efficiency is due to lower bending losses from a thin cross-section, low creep because of friction covers and high modulus of elasticity traction layers, and no wedging action into pulleys. Flat belts have thin cross-sections and wrap around pulleys easilyĪ significant advantage of flat belts is efficiency of nearly 99%, about 2.5-3% better than V-belts. This eliminates the need for high tension, lowering shaft and bearing loads. Modern flat belts are made with reinforced, rubberized fabric that provides strength and high friction levels with the pulley (Fig. There is no slip with this belt except for ratcheting or tooth jumping. Positive drive or synchronous belts rely on the engagement of teeth on the belt with grooves on the pulley. Flat belts are the purest form of friction drive while V-belts have a friction multiplying effect because of wedging action on the pulley. They require tension to maintain the right amount of friction. Friction drive belts rely on the friction between the belt and pulley to transmit power. Belt typesĪll power transmission belts are either friction drive or positive drive. Sheaves and pulleys are usually less expensive than chain drive sprockets and have little wear over long periods of operation. This availability reduces downtime and inventory. Replacement parts can be easily obtained from local distributors. When compared to other forms of power transmission, belts provide a good combination of flexibility, low cost, simple installation and maintenance, and minimal space requirements.īelt-driven equipment uses readily available components. Today, flat, V, and synchronous belting is still being used in power transmission. The need to eliminate speed variations led to the development of synchronous or toothed belts about 1950 and the later development of fabric-reinforced elastomer materials. This led to the development of the vulcanized rubber V-belt in 1917. Later, cotton or hemp rope was used with V-groove pulleys to reduce belt tension. The first belts were flat and ran on flat pulleys. Power transmission belting has been used for more than 200 years.
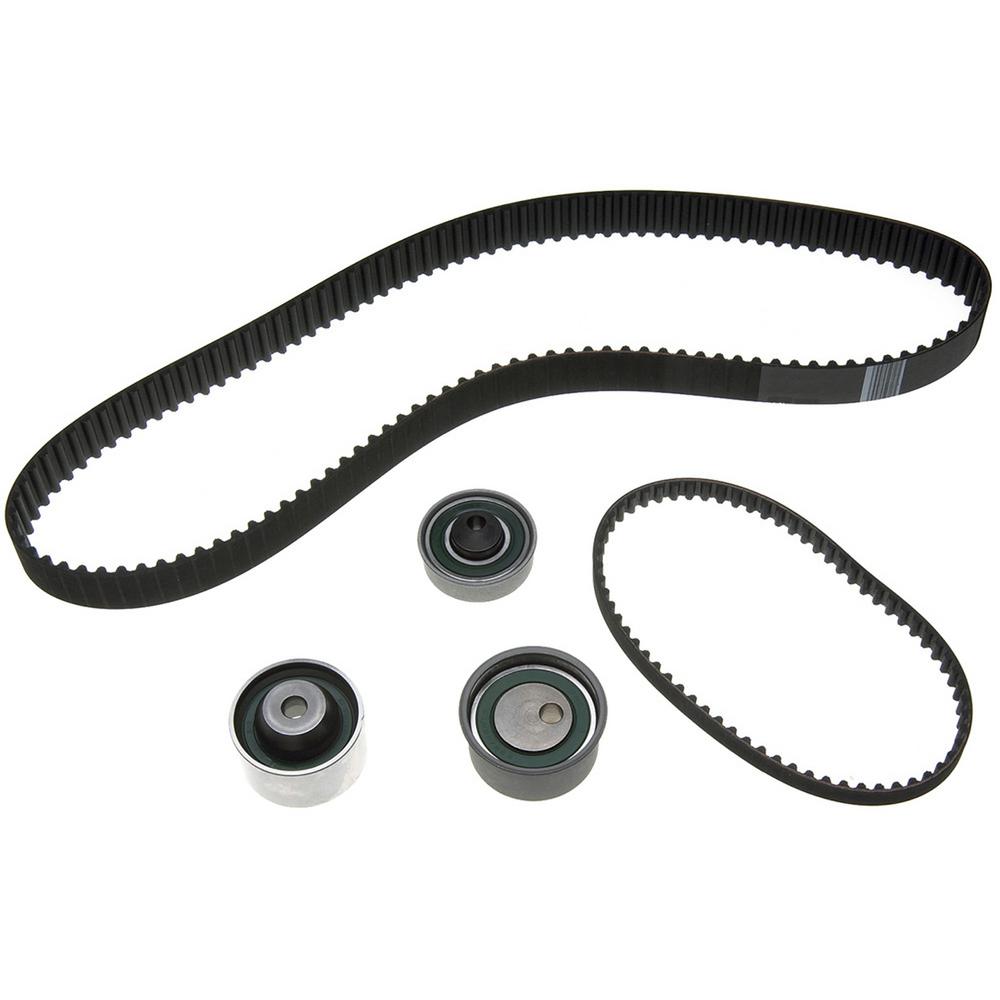
Misalignment is a common cause of premature belt failure. There are three basic types of power transmission belting: flat, V, and synchronous. For long life, select the belt type best suited for the application.
